Some Of Alcast Company
Table of ContentsOur Alcast Company Statements8 Simple Techniques For Alcast Company7 Easy Facts About Alcast Company ExplainedFacts About Alcast Company UncoveredIndicators on Alcast Company You Should KnowThe Ultimate Guide To Alcast Company
Chemical Comparison of Cast Light weight aluminum Alloys Silicon advertises castability by lowering the alloy's melting temperature level and boosting fluidity during spreading. Additionally, silicon contributes to the alloy's stamina and wear resistance, making it valuable in applications where sturdiness is crucial, such as vehicle components and engine parts.It additionally boosts the machinability of the alloy, making it much easier to refine right into completed products. In this way, iron adds to the overall workability of aluminum alloys.
Manganese adds to the stamina of light weight aluminum alloys and boosts workability (aluminum casting manufacturer). It is generally made use of in functioned aluminum products like sheets, extrusions, and profiles. The existence of manganese help in the alloy's formability and resistance to breaking during manufacture processes. Magnesium is a light-weight aspect that provides toughness and effect resistance to light weight aluminum alloys.
3 Easy Facts About Alcast Company Shown
It permits the production of lightweight components with excellent mechanical residential properties. Zinc improves the castability of light weight aluminum alloys and aids control the solidification process during spreading. It improves the alloy's strength and firmness. It is typically located in applications where intricate forms and great details are essential, such as decorative spreadings and certain vehicle parts.

The main thermal conductivity, tensile strength, return strength, and elongation differ. Select appropriate resources according to the performance of the target product created. Amongst the above alloys, A356 has the greatest thermal conductivity, and A380 and ADC12 have the most affordable. The tensile limitation is the opposite. A360 has the most effective yield toughness and the highest prolongation rate.
About Alcast Company
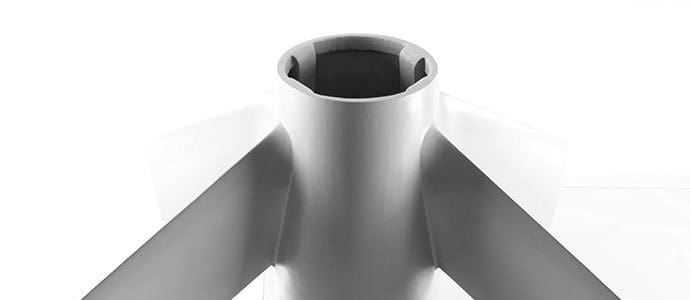
In accuracy casting, 6063 is fit for applications where elaborate geometries and top quality surface area finishes are paramount. Examples include telecommunication units, where the alloy's superior formability permits streamlined and visually pleasing designs while preserving architectural honesty. In the Illumination click for info Solutions sector, precision-cast 6063 elements develop sophisticated and effective illumination components that require detailed forms and excellent thermal performance.
The A360 shows exceptional elongation, making it excellent for facility and thin-walled parts. In precision casting applications, A360 is well-suited for markets such as Customer Electronic Devices, Telecommunication, and Power Tools.
Some Of Alcast Company
Its distinct homes make A360 a beneficial option for precision casting in these markets, improving product resilience and top quality. aluminum casting manufacturer. Aluminum alloy 380, or A380, is a commonly used casting alloy with numerous distinct features.
In accuracy casting, light weight aluminum 413 radiates in the Customer Electronics and Power Equipment sectors. This alloy's exceptional deterioration resistance makes it a superb option for outside applications, making sure lasting, sturdy products in the stated industries.
Getting The Alcast Company To Work
The aluminum alloy you choose will significantly influence both the casting procedure and the buildings of the last item. Because of this, you should make your decision thoroughly and take an informed method.
Determining the most suitable aluminum alloy for your application will certainly imply evaluating a vast variety of features. The initial classification addresses alloy features that affect the manufacturing process.
The Definitive Guide for Alcast Company
The alloy you choose for die spreading straight affects numerous aspects of the casting procedure, like how simple the alloy is to collaborate with and if it is prone to casting issues. Warm cracking, additionally referred to as solidification cracking, is a regular die casting problem for light weight aluminum alloys that can lead to inner or surface-level tears or fractures.
Particular light weight aluminum alloys are extra prone to warm breaking than others, and your option needs to consider this. Another common problem located in the die casting of aluminum is pass away soldering, which is when the actors stays with the die wall surfaces and makes ejection challenging. It can harm both the actors and the die, so you ought to search for alloys with high anti-soldering residential or commercial properties.
Deterioration resistance, which is currently a significant feature of aluminum, can vary substantially from alloy to alloy and is a crucial particular to take into consideration depending on the ecological problems your product will certainly be subjected to (Casting Foundry). Put on resistance is an additional residential property typically sought in light weight aluminum items and can differentiate some alloys